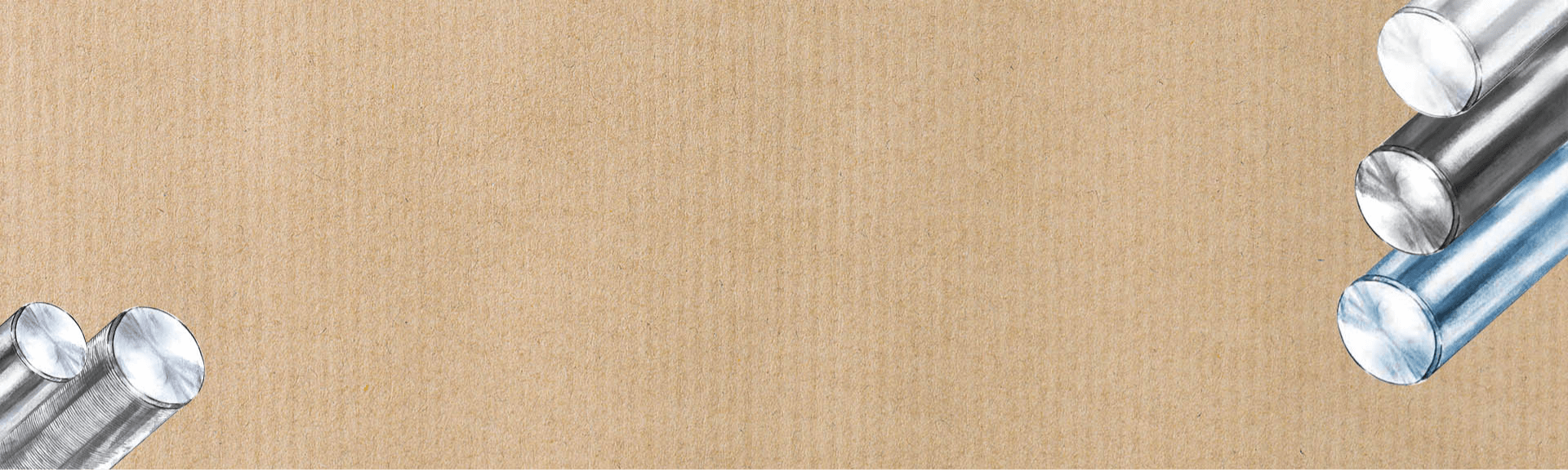
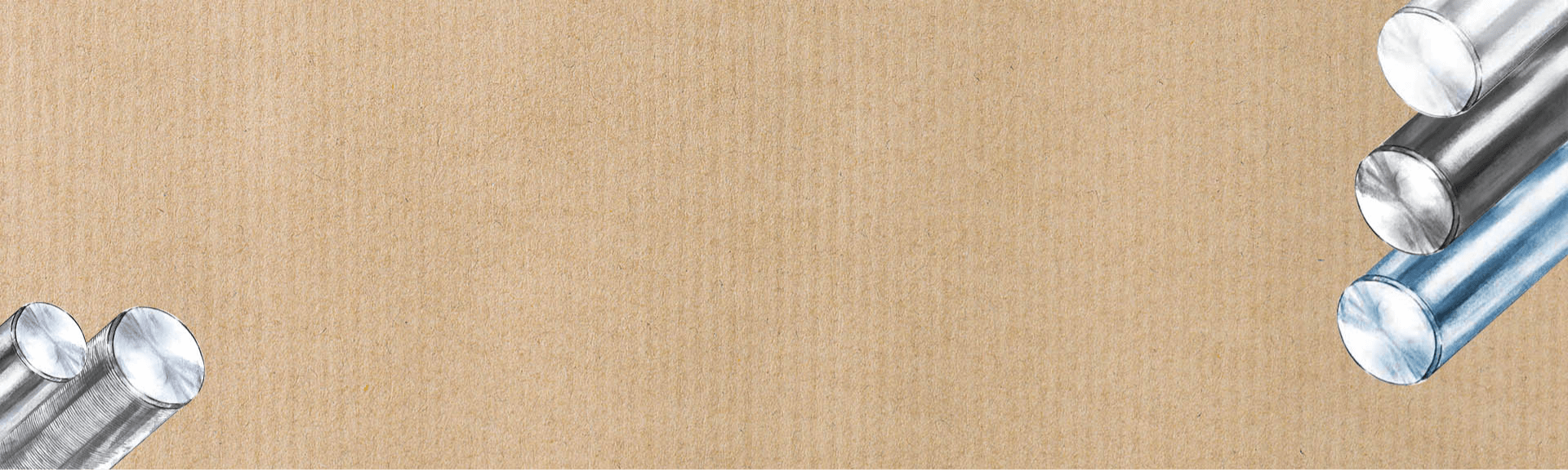
Glatte Rakelwellen
Hydrodynamische Dosierung
Bei der Dosierung arbeiten glatte Rakelwellen – analog zu Streichklingen – nach dem hydrodynamischen Prinzip: Entscheidend für die Menge des Auftrags ist der Druck in der Dosierzone.
Dieser Druck folgt den Gesetzen der Strömungsmechanik:
- Maschinengeschwindigkeit
- Geometrie (Durchmesser) des Dosiersystems
- Farbrheologie
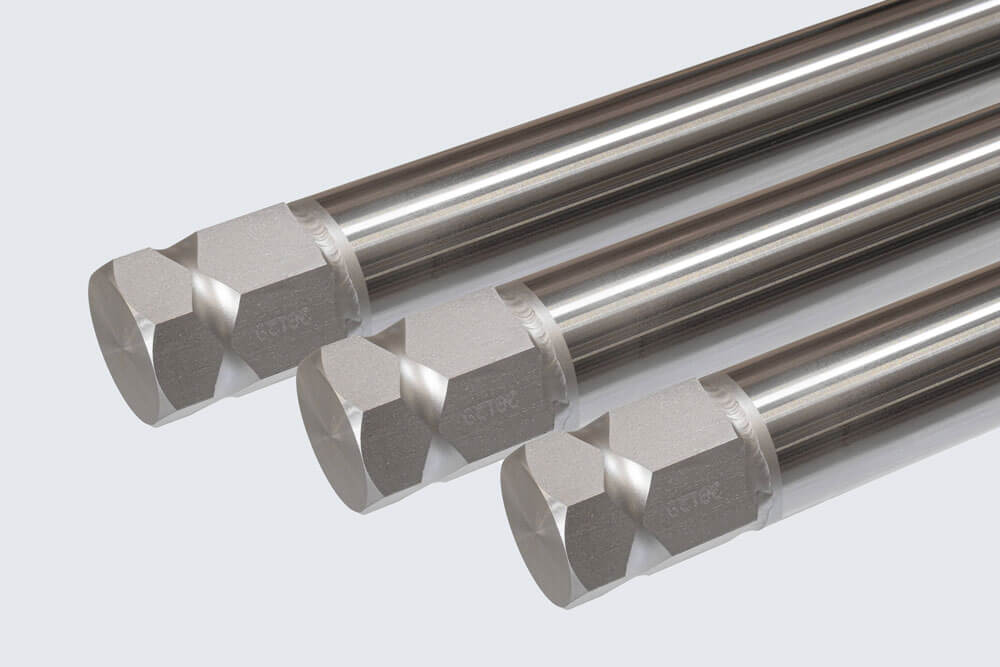
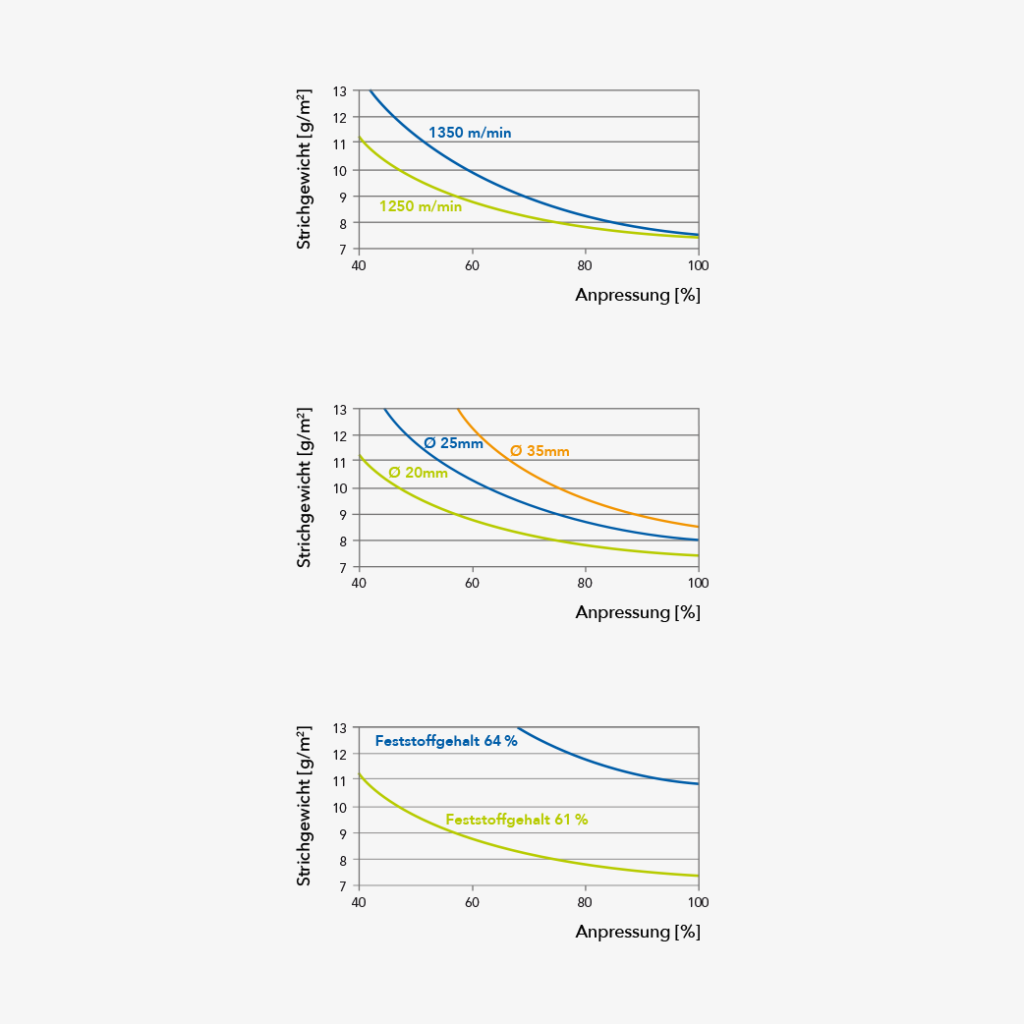
Bei einer Erhöhung der Maschinengeschwindigkeit um 100 m / min kann sich das Strichgewicht um knapp 10 % von 8 g / m² auf 8,8 g / m² erhöhen.
Größere Durchmesser führen ebenfalls zu höheren Strichgewichten: 5 mm Durchmesser-Zuwachs bringen ca. 10 % mehr Strichauftrag.
Meist ist die Farbrheologie bzw. der Feststoffgehalt die dominante Größe für das Auftragsgewicht: Eine „relativ“ kleine Anhebung des Feststoffgehalts um ca. 3 % kann das Auftraggewicht um ca. 50 % erhöhen.
Stabile Produktionsbedingungen sind in der Praxis nur bei vergleichsweise hohen Anpressdrücken möglich. Wird die Auftragmenge über einen zu geringen Anpressdruck erhöht, treten Schwankungen im Auftragsgewicht auf.
Anwendungsbeispiele für glatte Rakel
Vorstrich bei grafischen Papieren mit der Filmpresse
Hier werden glatte Rakelwellen mit Durchmessern von 15 bis 38 mm bevorzugt. Insbesondere bei hohen Maschinengeschwindigkeiten und höchsten Feststoffgehalten haben sich glatte Rakelausführung durchgesetzt.
In der Praxis können verchromte Rakel Standzeiten von ca. zwei Wochen erreichen. Bei keramikbeschichteten Rakeln beträgt die Standzeit bis über vier Wochen.
Streichen von Faltschachteln, Flaschenträgerkartons, Linern
Glatte Rakel mit Durchmessern von 10 und 12 mm werden hier schon seit Jahrzehnten, meist im Vorstrich und auf der Rückseite, eingesetzt. Wegen des ausgeprägten Randverschleißes verfügen die eingesetzten Rakel oft über eine extra starke Chromschicht oder eine Keramikbeschichtung.
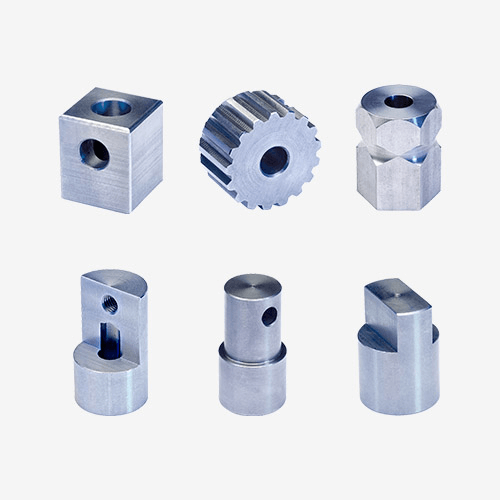
Mehr erfahren+ Zuklappen-
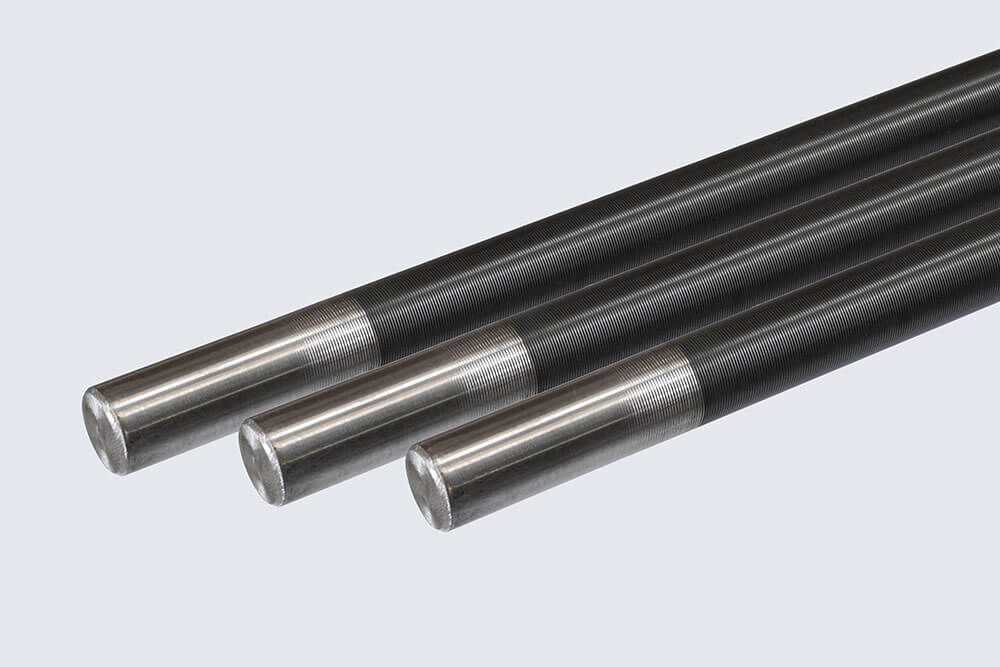
Profilierte
Rakelwellen
Volumetrische Dosierung
Als volumetrische Dosierung wird die Dosierung mit profilierten Rakelwellen bezeichnet. Während des Dosiervorgangs berühren die Spitzen des Profils nahezu die Papierbahn bzw. die Auftragswalze. Die Geometrie des Profils, also der Rillenquerschnitt und -abstand, bestimmt die exakte Auftragsmenge.
Zudem hat die Profilgestaltung Einfluss auf die Qualität des Auftrags sowie auf die Standzeit. Auf Basis unserer Erfahrungen lässt sich das Profil für jeden Anwendungsfall optimieren. Wir bieten Profile für einen Dosierbereich von 3 - 150 ml / m an – also auch für die gängigsten Dosierungen von 15 - 50 ml / m.
Bei profilierten Rakeln dient die Anpresskraft weniger zur Einstellung der Auftragmenge als zur Verschleißkompensation. Idealerweise wird direkt nach der Installation einer neuen Dosiereinheit ein hoher Anpressdruck gefahren und dieser kontinuierlich bis zum Erreichen des Mindestdrucks reduziert. So bleibt die Auftragsmenge bei maximaler Standzeit des Dosiersystems konstant.
Unsere Versuchsreihen, Laborauswertungen und jahrzehntelange Erfahrung ermöglichen es unseren Kunden, ihre Auftragsprozesse gezielt zu optimieren:
- höhere Gleichmäßigkeit im Auftrag = höhere Qualität
- längere Standzeiten = mehr Wirtschaftlichkeit
- intelligentere Konstruktion = neue Möglichkeiten für innovative Papier-Produkte
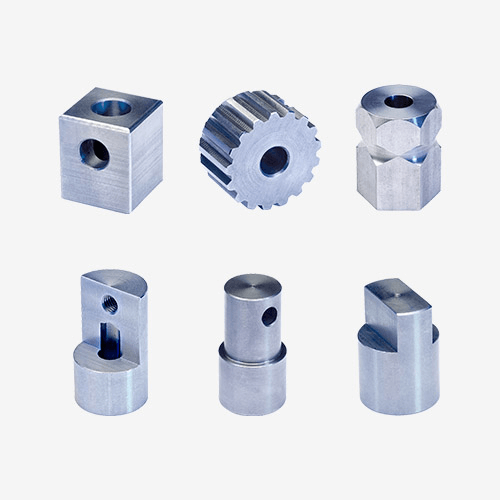
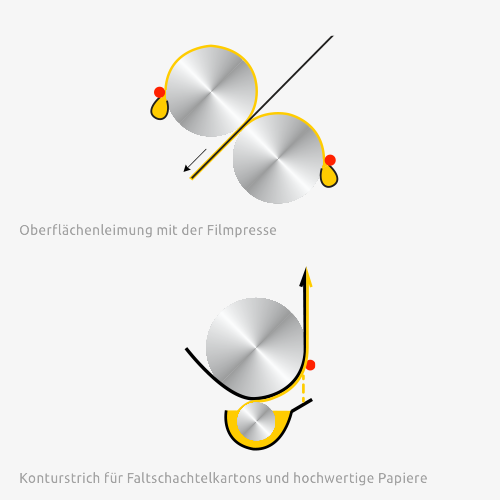
Anwendungsbeispiele für Profilrakel
Oberflächenleimung mit der Filmpresse
Sicherlich die wichtigste Anwendung für die profilierte, verchromte Rakelwelle mit einem Durchmesser von 10 bis 15 mm. Im Gegensatz zur glatten Rakelwelle ist die profilierte Welle in einem äußerst großen Viskositätsbereich einsetzbar, womit sie sich bestens für sehr niedrigviskose Stärkelösungen eignet. Standzeiten von bis zu vier Wochen im 24 / 7 Betrieb lassen sich problemlos erreichen, wenn die Stärkeflotte weitestgehend frei von abrasiven Bestandteilen ist.
Konturstrich für Faltschachtelkartons und hochwertige Papiere
Für eine sehr gleichmäßige Strichverteilung und -abdeckung kommen zunehmend Profilrakelwellen zum Einsatz. Sie erzielen Strichergebnisse, deren Qualität mit der von traditionellen Luftmessern oder modernen Vorhangstreichaggregaten vergleichbar ist. Bei richtiger Einstellung aller Parameter erzielen insbesondere keramikbeschichtete Wellen sehr wirtschaftliche Standzeiten.
Mehr erfahren+ Zuklappen-
Größere Rakeldurchmesser
Ideal für mehr Produktivität
Üblicherweise werden Rakelwellen mit Durchmessern von 10 bis 15 mm und glatten Oberflächen im Direktauftrag bzw. mit profilierten Oberflächen in der Filmpresse eingesetzt. Abhängig vom Anteil abrasiver Bestandteile in den Streichmedien sind Standzeiten von zwei bis vier Wochen erreichbar. All das ist gängige Praxis bei Papiermaschinen auf der ganzen Welt. Doch in einem immer härteren Wettbewerb zählt jede zusätzliche Produktionsstunde und das Minimieren von Ausschuss.
Also müssen Rakelwellen höhere Standzeiten und seltenere Revisionszyklen bieten. Die technologisch einfache Lösung dafür ist das Einsetzen von Rakelwellen mit größerem Durchmesser.
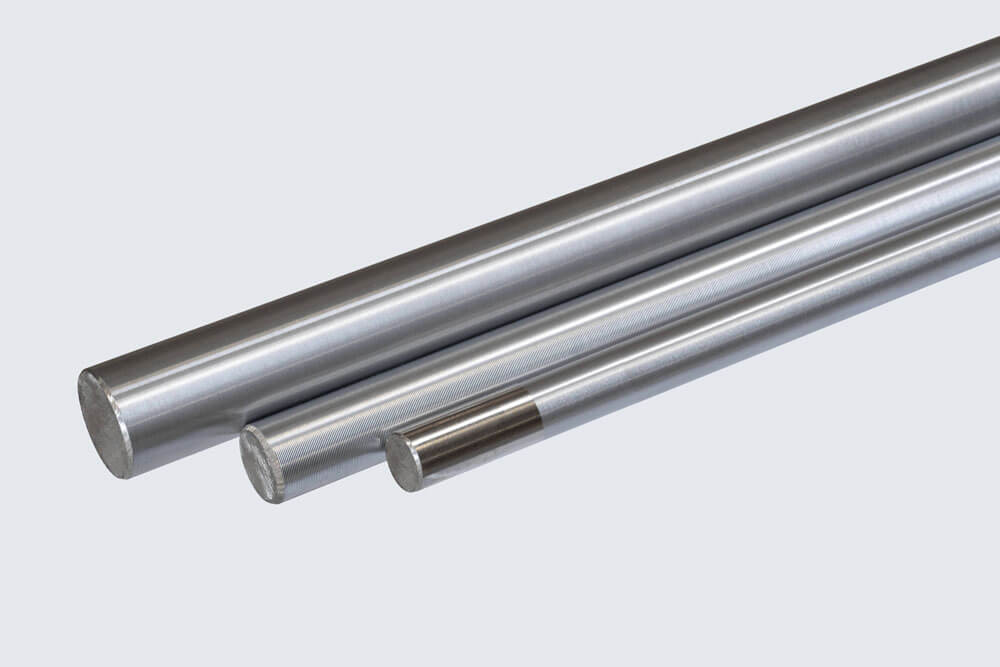
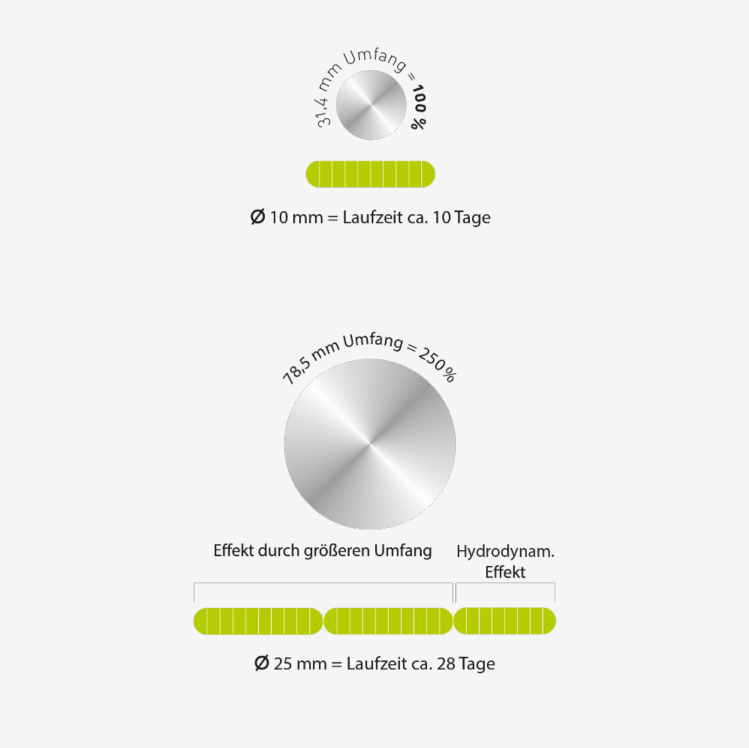
Die Effekte
Die für den Verschleiß verantwortlichen Kräfte wirken auf eine größere Fläche ein – die Rakel halten der Belastung länger Stand.
Die Anpresskraft der Rakelwelle gegen die Papierbahn oder die Gegenwalze ist gleichmäßig und schonend. Das vermeidet das „Eingraben“ der Welle, reduziert die Verformung und verlängert die Lebensdauer des Gegenwalzenbezuges.
Es entsteht ein hydrodynamischer Prozess zwischen Rakel und Papierbahn, ähnlich dem Aquaplaning beim Autofahren – nur dass er hier wünschenswert ist: Ein dünner Flüssigkeitsfilm reduziert die Reibung und damit den Verschleiß der Rakel praktisch auf Null.
Während die ersten beiden Effekte proportionale Auswirkungen auf die Standzeiten der Rakel haben, sorgen die hydrodynamischen Effekte für eine deutlich überproportionale Laufzeitverlängerung. Zudem sind Rakelwellen mit größeren Durchmessern deutlich widerstandsfähiger gegen Papierbahnriss, unrund laufende Antriebe und unsachgemäße Handhabung.
Mehr erfahren+ Zuklappen-
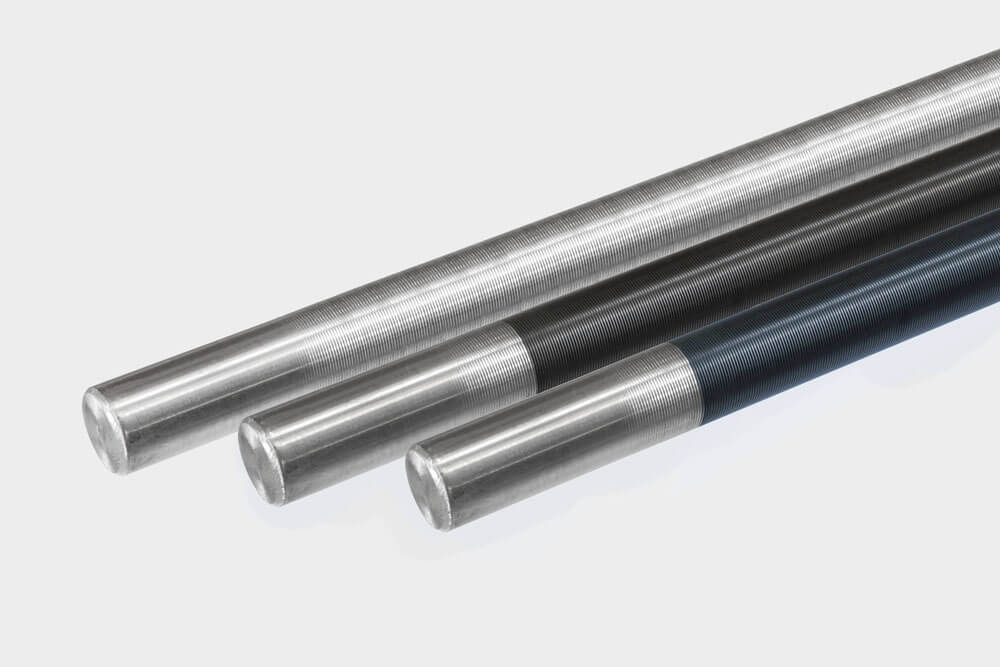
Chrom, Keramik, Karbid
Spezialisten für Verschleissfestigkeit
Die Weiterentwicklung bewährter Herstellungsverfahren sowie Materialinnovationen führen zu mehr Verschleißfestigkeit und damit zu mehr Wettbewerbsfähigkeit. Das gilt beispielsweise für das Hartverchromen oder das keramische Beschichten von Verschleißteilen.
Letztlich bestimmen Einsatzzweck und Einsatzziel die Auswahl:
- Chrombeschichtungen – die wirtschaftlichste Lösung für viele Anwendungen
- Keramikoberflächen – für anspruchsvolle Prozesse mit abrasiven Effekten
- Karbid – wenn Homogenität & Verschleißfestigkeit entscheidend sind
Welche Oberflächenvergütung für einen bestimmten Prozess ideal ist, lässt sich dennoch nicht pauschal sagen, da es sehr unterschiedliche Prozessparameter gibt:
- Zusammensetzung des Papiers
- Inhaltsstoffe des Streichmediums
- Auftragsart (direkt oder indirekt)
- Produktionsbedingungen der Papier- und Streichmaschinen
- Rakelwelle (Durchmesser; profiliert oder glatt)
Als Spezialist für Dosiersysteme konzentrieren wir uns voll auf diese Aspekte der Papierproduktion. Dazu gehört auch eine Beratungsqualität, die ihresgleichen sucht.
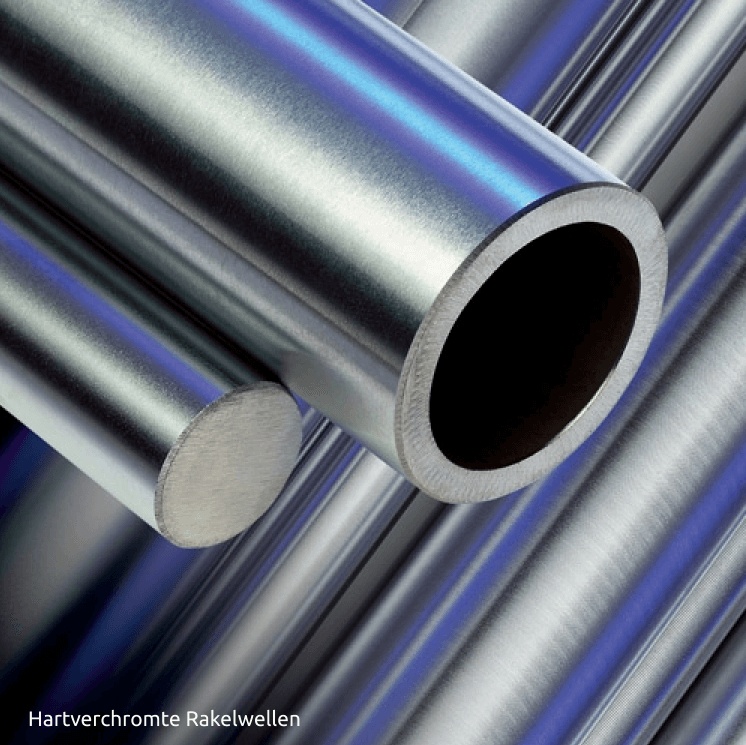
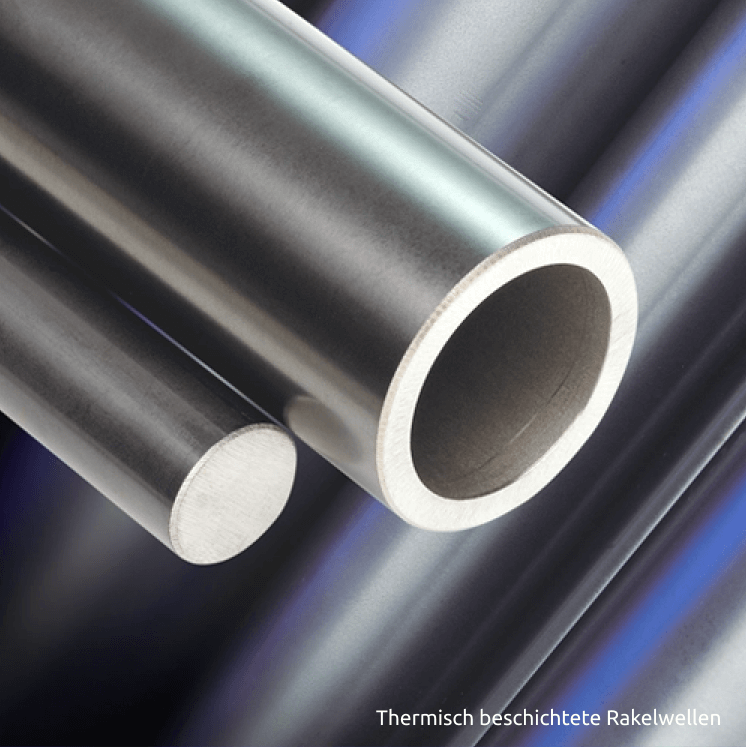
Oberflächenvergütung im Vergleich
Hartverchromte Rakelwellen
Galvanische Auftragsverfahren ermöglichen eine gleichmäßige Schichtstärke über die gesamte Oberfläche. Das ist besonders bei profilierten Rakelwellen mit steilen Winkelgeometrien ein großer Vorteil.
Thermisch beschichtete Rakelwellen
Keramische Beschichtungen werden im Plasma- oder Hochgeschwindigkeits-Spritzverfahren aufgetragen. Die Oberflächen der neuen Rakelgeneration sind deutlich verschleißfester, was ihre Standzeiten um das drei- bis siebenfache verlängert.
Mehr erfahren+ Zuklappen-